Quality Inspector
Wise Staffing Group
Spring Hill, TN
- Full-Time
Job Description
Company Info
Job Description
Qualifications:
Deep Understanding of Primary Quality Management Systems
Highly competent with Quality Tools and Methodologies
Extensive experience with Power Point and Creation of Excel Spreadsheets
Expert Problem Solver
Leader in Root Cause Analysis
Experienced in COPQ Reduction
Responsibilities:
Forms relationships with Customer Quality and Manufacturing teams
Understands and adheres to safety guidelines in production.
Proactively audits incoming material for potential issues.
Provides quick feedback of issues in Customer Facility to supplier, with details and pictures that can assist supplier in quickly containing and
Ensures inspection processes are followed, certified products are quickly provided to production lines and clean points are communicated and monitored.
Verifies accuracy of containment data and inspection findings
Maintains inventory of rejected parts for accurate RMA processing.
Works with customers to establish boundaries and samples for non-conformances.
Creates Work Instructions and obtains Supplier/Customer approval for Containments to ensure effectiveness.
Ability to negotiate with the customer on the Suppliers behalf to reduce PPM, Scrap and present the
Can present basic root cause findings/countermeasure from supplier to Customer facilities and OEMs.
Attends Customer meetings, and provides feedback on clean points, part issue resolution, and data.
Provides on-site support, diagnostics, and professional responsibilities for all quality issues/concerns for customer.
Reports as necessary on changes in processes (internally and externally initiated) and on performance.
Plans, performs, and participates in all levels of testing to help in root cause analysis
Capable of performing DOE to eliminate or identify multiple potential root causes to the failure.
Ensures root cause investigation tools (8D/5P) are completed, approved, and presented to
Drives Corrective Action Resolution activities.
Works directly with Customer/OEM engineers to assist in root cause analysis – Leads root cause.
Approves 8D/5P from supplier, presents details to Customer/OEM, tracks countermeasure.
Develops Effective Firewall Activities and both Supplier and Customer Facilities
Uses quality disciplines to effectively reduce COPQ.
Job Description
Forms relationships with Customer Quality and Manufacturing teams
• Understands and adheres to safety guidelines in the production environment
• Proactively audits incoming material for potential issues
• Provides quick feedback of issues in Customer Facility to supplier, with details and pictures that can assist supplier in quickly containing and certifying product
• Ensures inspection processes are followed, certified product is quickly provided to production lines and clean points are communicated and monitored
• Initiates, trains personnel and helps coordinate containment/sort/rework when requested
• Verifies accuracy of containment data and inspection findings
• Maintains inventory of rejected parts for accurate RMA processing.
• Works with customers to establish boundaries and samples for non-conformances.
• Creates Work Instructions and obtains Supplier/Customer approval for Containments to ensure effective inspections.
• Ability to negotiate with the customer on the Suppliers behalf to reduce PPM, Scrap and present the supplier’s position
• Can present basic root cause findings/countermeasure from supplier to Customer facilities and OEMs
• Attends Customer meetings, and provides feedback on clean points, part issue resolution, and data
• Provides on-site support, diagnostics, and professional responsibilities for all quality issues/concerns for customer
• Reports as necessary on changes in processes (internally and externally initiated) and on performance standards Plans, performs, and participates in all levels of testing to help in root cause analysis
• Capable of performing DOE to eliminate or identify multiple potential root causes to the failure
• Ensures root cause investigation tools (8D/5P) are completed, approved, and presented to stakeholders
• Drives Corrective Action Resolution activities
• Works directly with Customer/OEM engineers to assist in root cause analysis – Leads root cause analysis for supplier
• Approves 8D/5P from supplier, presents details to Customer/OEM, tracks countermeasure effectiveness
• Develops Effective Firewall Activities and both Supplier and Customer Facilities
• Uses quality disciplines to effectively reduce COPQ Skills
• Experienced Manager or Engineer within Manufacturing
• Deep Understanding of Primary Quality Management Systems
• Highly competent with Quality Tools and Methodologies
• Extensive experience with Power Point and Creation of Excel Spreadsheets
• Use of Minitab or equivalent programs
• Expert Problem Solver
• Leader in Root Cause Analysis
• Experienced in COPQ Reduction
Shift times will vary depending on current needs and will consist of 8,10,12, and or 14-hour shifts.
Must have open flexibility.
How can the hiring manager reach you?
You Already Have an Account
We're sending an email you can use to verify and access your account.
If you know your password, you can go to the sign in page.
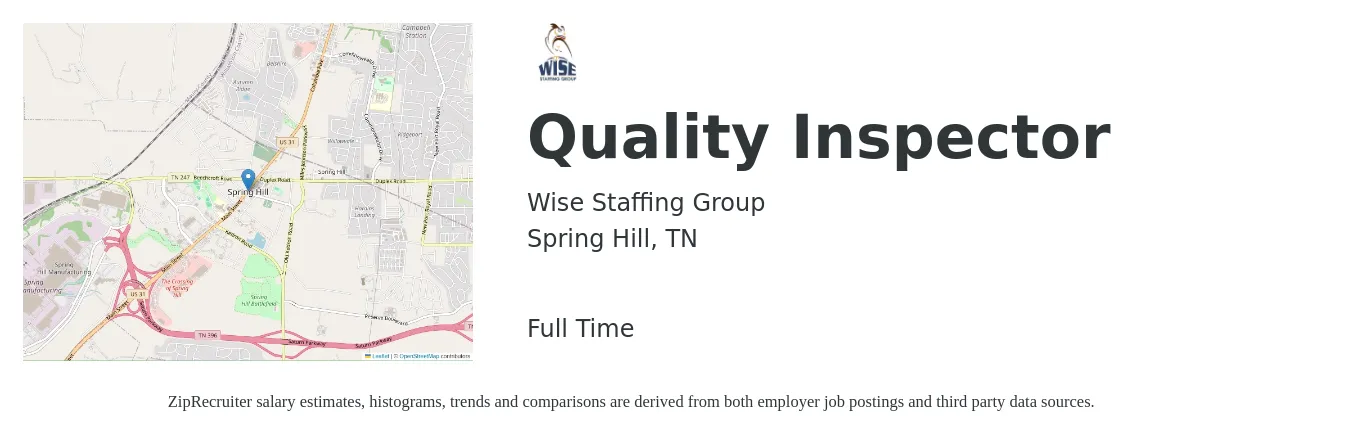